Содержание
Введение . . . . . . . . . .
. . . . . . . . . . . . . . . . . . . . . . . . . . . . . .
. . . . . . . . . . . . . . . . . 4
1.
Краткая техническая характеристика ВАЗ-2106 . . . . .
. . . . . . . . . . . . . . . . . 7
2.
Назначение, устройство и принцип работы передней
подвески
автомобиля ВАЗ-2106 . .
. . . . . . . . . . . . . . . . . . . . . . . . . . . . . .
. . . . . . . . . . . .8
3.
Техническое обслуживание и ремонт передней подвески .
. . . . . . . . . . . . . 13
3.1.
Определение состояния деталей передней подвески . . .
. . . . . . . . . . . . . 13
3.2.
Проверка и регулировка углов установки передних колес
. . . . . . . . . . . .17
3.3.
Инструменты и приспособления для ТО и ремонта
передней подвески .37
5.
Техника безопасности и противопожарные мероприятия .
. . . . . . . . . . . . . . 38
6.
Список использованной литературы . . . . . . . . . .
. . . . . . . . . . . . . . . . . . . . . . .43
|
|
|
|
|
|
|
|
|
|
|
|
Изм. |
Лист |
№ докум. |
Подпись |
Дата |
|
|
|
|
Передняя подвеска ВАЗ 2106 |
Лит. |
Лист |
Листов |
|
|
|
|
|
|
|
2 |
43 |
|
|
|
|
|
|
|
|
|
|
|
|
|
Введение.
РАЗВИТИЕ АВТОМОБИЛЕСТРОЕНИЯ:
Автомобильный
транспорт занимает одно из ведущих мест в единой
транспортной системе
России. Развитие автомобилестроения в том недалеком СССР
относится к 1931-1932 годам, когда вступили в действие
реконструированный завод АМО и вновь построенный ГАЗ. На них
было организовано
массовое производство грузовых автомобилей ГАЗ-АА и ЗИЛ-5.
В 1940 году начал производство малолитражных автомобилей
московский
завод имени КИН ныне АЗЛК. За годы послевоенных пятилеток
вступили в строй Кутаисский (КАЗ), Кременчугский (КрАЗ),
Ульяновский (УАЗ), Минский (МАЗ) автомобильные заводы,
Павловский (ПАЗ), Ликинский
(ЛиАЗ), и Львовский (ЛАЗ) автобусные заводы, а также другие
автомобильные заводы, производящие автомобили - самосвалы и
прицепно - подвижной состав.
С каждым годом растет производство автомобилей, но
одновременно с ростом числа автомобилей, увеличивается
загрязнение окружающей среды выхлопами, отработавшими газами
(ОГ) и существенно вырастает шум, производимый ими.
Токсичность отработавших газов, выбрасываемых в
атмосферу при работе карбюраторных двигателей,
обуславливается главным
образом,
содержание оксида углерода (СО), окиси азота (NО), и
соединениями свинца
(РЬ), а дизелей - содержанием окислов азота и сажи
(С).
Большое значение для уменьшения загрязнения окружающего
воздуха отработавшими газами приобретает ежедневно
техническое обслуживание подвижного состава автомобильного
транспорта, находящегося в эксплуатации, одной из основных
задач которого является контроль
содержания токсичных веществ в выхлопных газах и доведение
его до норм,
установленных
в России.
На автомобильных заводах для снижения токсичности
отработавших газов
разрабатываются новые модели двигателей и мероприятия по
совершенствованию рабочего процесса в двигателе, выбору
оптимальных
режимов его работы и оптимизации параметров систем питания и
зажигания.
Значительное уменьшение токсичности может быть достигнуто
также нейтра- |
|
|
|
|
|
|
Лист |
|
|
|
|
|
3 |
Изм. |
Лист |
№ документа |
Подпись |
Дата |
лизацией токсичных веществ при помощи специальных
дожигателей
отработавших газов, устанавливаемых на автомобилях.
Частичным решением
данной проблемы является и оснащение автотранспортных
средств дизельными двигателями, т.е. дизеляция автомобилей,
которая позволяет значительно сократить расход топлива и
снизить токсичность отработавших
газов.
Последнее объясняется тем, что в топливе для дизелей не
содержится
свинцовых присадок, а выброс вредных компонентов, таких, как
углеводород
и окись углерода, несколько раз ниже. Кроме того, дизель на
25-30% экономичнее карбюраторного двигателя. Для
производство дизельного топлива требуется примерно в 2,5
раза меньше затрат, чем для производства бензина и срок
службы современного дизеля примерно в 1,5 раза выше
карбюраторного двигателя. Расширение дизеляции происходит
благодаря росту выпуска дизелей на Камском автомобильном
заводе (КамАЗ),
Ярославском моторном заводе (ЯМЗ) и Кутаинском автозаводе
(КАЗ). Кроме
того, созданы новые дизели для авто ЗИЛ и ГАЗ и подготовлены
производственные мощности для массовой дизеляции современных
легковых
автомобилей. Одновременно с этим намечается расширение
производства автомобилей, работающих на сжатом и сжиженном
газах.
Перевод автомобиля с жидкого на газообразное топливо
экономически оправдано, т.к. стоимость газового топлива
примерно в 2-2,5 раза меньше
стоимости бензина. По сравнению с карбюраторными двигателями
продуты
сгорания двигателей, работающих на газе, содержат
значительно меньше
токсичных веществ.
Сильный шум при движении автотранспортных средств возникает
в результате выброса в атмосферу отработавших газов и
взаимодействия шин с дорогой. Поэтому основными
направлениями работ по снижению уровня шума, создаваемого
автотранспортными средствами является усовершенствование
конструкции глушителей и шин.
В общем балансе шума, создаваемом автомобилями, значительная
роль принадлежит несущей системе (кузову или раме), а также
элементам подвески. |
|
|
|
|
|
|
Лист |
|
|
|
|
|
4 |
Изм. |
Лист |
№ документа |
Подпись |
Дата |
Шум от несущей системы возникает в результате ее вибрации
при движении автомобиля и работе двигателя. Для снижения
шума внутренние поверхности и основание кузова легкового
автомобиля покрывают
вибропоглащающими пастами. Вибрацию несущей системы,
возникающей от
толчков при движении по неравномерностям дорог снижают
рессорами или подвесками специальной конструкции, в
частности пневматическими. Автомобильные заводы постоянно
работают над совершенствованием конструкций грузовых
автомобилей и автопоездов, т.е. повышением их
эксплуатационных качеств, производительности, и
приспособленности к использованию прицепов и полуприцепов,
уменьшению расхода топлива и смазочных материалов. К
основным направлениям развития конструкций легковых
автомобилей следует отнести переход на выпуск
переднеприводных автомобилей с уменьшенной массой,
снабженные двигателями с рабочим объемом до 1,8 литров.
Уменьшение массы переднеприводных автомобилей позволяет
снизить расход топлива на 10-15%.
Совершенствуется и структура автомобильного парка:
•
увеличивается выпуск специализированных автомобилей,
прицепов и
полуприцепов, автомобилей до двух тонн и более восьми тонн;
•
уменьшается выпуск автомобилей грузоподъемностью от двух до
пяти
тонн;
Однако все эти усовершенствования смогут быть в полной мере
реализованы только при условии грамотной эксплуатации
автотранспортных средств, которая в основном зависит от
водителя, от его знания конструкции автомобили, умения
своевременно обнаружить и устранить неисправности и
от его мастерства вождения.
Основными направлениями экономического и социального
развития на
период до 2000 года предусматривается уменьшение на 15-25%
удельную
металлоемкость, увеличить ресурсы работы и снизить
трудоемкость технического обслуживания автомобилей. Эти
задачи связаны в первую
очередь с повышением качества и эффективности работ по
техническому обслу- |
|
|
|
|
|
|
Лист |
|
|
|
|
|
5 |
Изм. |
Лист |
№ документа |
Подпись |
Дата |
живанию с применением более совершенных средств и методов
обслуживания и ремонта автомобилей.
На автотранспортных предприятиях по техническому
обслуживанию автомобилей все шире внедряется средства
диагностирования и новые
формы организации труда: бригадный подряд, оценка трудовой
деятельности
по конечному результату и др. Все это требует ускоренного
развития МТБ предприятий, дальнейшего совершенствования
процессов технического обслуживая и ремонта автомобилей,
внедрения более широкой механизации выполняемых работ и
улучшения организации производства. Механизация работ
облегчает и ускоряет многие технологические процессы,
поэтому от
рабочих, обслуживающих автомобили, сейчас требуется не
только знание их
устройства, но и практические навыки пользования современным
оборудованием, умение применять необходимые приспособления,
инструменты, КИАП при диагностировании автомобилей.
Применение современного оборудования при техническом
обслуживании и ремонте не исключает выполнения общеслесарных
операций, которыми
должен владеть каждый рабочий-ремонтник. Слесарь по ремонту
автомобиля
должен иметь четкие представления об основных методах и
способах восстановления деталей, технологии ремонтных работ,
включая вопросы сборки и испытания автомобилей после
капитального ремонта. |
|
|
|
|
|
|
Лист |
|
|
|
|
|
6 |
Изм. |
Лист |
№ документа |
Подпись |
Дата |
1.
Краткая техническая характеристика ВАЗ-2106.
показатели |
ВАЗ-2106 |
Общие данные |
Количество мест |
5 |
Полезная нагрузка,
кг |
400 |
Снаряженная масса
автомобиля, кг |
1 035 |
Габаритные размеры,
длина х ширина х высота, мм |
4 166 х 1 611 х 1
440 |
Максимальная
скорость, км/ч:
с полной массой
с водителем и
пассажиром |
148
150 |
Время разгона с
места до 100 км/ч, с:
с полной массой
с водителем и
пассажиром |
17,5
16 |
Двигатель
|
Модель |
2106 |
Тип |
Четырехтактный,
бензино-вый, карбюраторный |
Количество и
расположение цилиндров |
Четыре в ряд |
Рабочий объем, л |
1,568 |
Номинальная мощность
при частоте вращения коленчатого вала 5600 мин-1,
кВт (л.с.)
по ГОСТ 14846-81 |
55,5 (75,5) |
Порядок работы
цилиндров |
1-3-4-2 |
Ходовая часть |
Передняя подвеска |
Независимая, на
попере-чных рычагах, с цилин-дрическими пружинами,
телескопическими гидрав-лическими амортизаторами и
стабилизатором попереч-ной устойчивости |
Задняя подвеска |
Зависимая, жесткая
балка, связанная с кузовом одной поперечной и
четырьмя продольными штангами, с цилиндрическими
пружи-нами и телескопическими амортизаторами |
Колеса |
Дисковые,
штампованные |
Размер обода |
12J-330
(5J-13) |
шины |
Камерные, радиальные
165/80R13
или 175/70R13 |
|
|
|
|
|
|
|
Лист |
|
|
|
|
|
7 |
Изм. |
Лист |
№ документа |
Подпись |
Дата |
2.
Назначение, устройство и принцип работы передней
подвески автомобиля ВАЗ-2106.
Подвески автомобиля обеспечивают уменьшение динамических
нагрузок, передаваемых от колес на кузов автомобиля, его
устойчивость,
плавность хода и гасят колебания кузова.
Общее устройство передней подвески и углы установки передних
колес. На легковых автомобилях применяется независимая
подвеска
передних колес, при которой перемещение одного из колес
практически
не зависит от другого.
Однорычажная подвеска передних колес типа «качающаяся свеча»
или по
имени ее изобретателя — «Мак-Ферсон» (рис. 1,), применяемая
на переднеприводных автомобилях, включает в себя телескопические
гидравлические амортизаторные стойки 3, витые
цилиндрические пружины 2, поперечные рычаги 6 и стабилизатор
поперечной устойчивости
1. Преимуществами подвески передних
колес типа «Мак-Ферсон»
являются простота ее конструкции, компактность,
значительное расстояние между опорами пружин, снижающее
передаваемое от них на кузов усилие, минимальное число
шарнирных
соединений в подвеске.
На автомобилях
с классической схемой компоновки устанавливаются
рычажно-пружинные бесшкворневая (автомобили ВАЗ-2105
и ИЖ-21251) или
шкворневая (автомобиль ГАЗ-31029) подвески.
Двухрычажная бесшкворневая подвеска передних колес
автомобилей
ВАЗ-2105 и ИЖ-21251 (рис. 1,) состоит из верхнего 8 и
нижнего 13 рычагов,
крепящихся с одной стороны на осях 17 соответственно
к кузову автомобиля (у автомобиля ВАЗ-2105) или
к опоре поперечины 16 (у
автомобиля ИЖ-21251) и к поперечине 16 подвески, а с другой
стороны — при помощи верхнего 9 и
нижнего 12 шаровых
шарниров к поворотной стойке 10 колеса.
Между нижним рычагом и
кузовом (на автомобиле ВАЗ-2105) или поперечиной подвески
(на автомобиле ИЖ-21251) размещена пружина,
внутри которой установлен амортизатор. |
|
|
|
|
|
|
Лист |
|
|
|
|
|
8 |
Изм. |
Лист |
№ документа |
Подпись |
Дата |
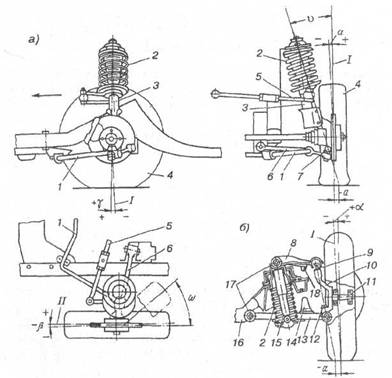
Рис.1.
Принципиальные схемы устройства передних подвесок и углы
установки передних колес:
а
— подвеска типа «Мак-Ферсон» переднеприводных автомобилей; б
— рычаж-но-пружинная
бесшкворневая подвеска автомобилей ВАЗ-2105 и ИЖ-21251;
1 — стабилизатор поперечной устойчивости; 2 — пружина; 3 —
телескопическая
стойка; 4 — передние колеса; 5 — рулевая тяга; 6 — рычаг
подвески; 7 — шаровая
опора; 8 и 13 — верхний и нижний рычаги; 9 и 12 — верхний и
нижний
шаровые шарниры; 10 и 11 — соответственно поворотные стойка
и цапфа с
осью; 14 и 18 — резиновые буферы сжатия и отбоя; 15 —
амортизатор; 16 —
поперечина; 17 — оси рычагов;
I
— вертикаль;
II
— колея; α — угол развала
колес; β — угол схождения колес; γ — угол продольного
наклона оси поворота колеса; ω — угол поворота колеса; υ —
угол поперечного наклона оси поворота
колеса; а — плечо обката колеса
В целях повышения устойчивости и управляемости автомобиля
при движении, а также уменьшения изнашивания шин, передние
управляемые колеса устанавливаются под определенными
углами, которые называются углами установки колес.
|
|
|
|
|
|
|
Лист |
|
|
|
|
|
9 |
Изм. |
Лист |
№ документа |
Подпись |
Дата |
Угол развала колес (а) характеризует отклонение плоскости
вращения каждого колеса от вертикали.
Угол схождения
колес (р) характеризует отклонение плоскости
вращения каждого
переднего колеса от направления движения
автомобиля (колеса).
Углы продольного у и поперечного и наклона оси поворота
колес характеризуют отклонение оси поворота (линии, проходящей
через середину верхней опоры телескопической стойки и
центр сферы шарнира на рычаге подвески типа «Мак-Ферсон»
или через центры шарниров двухрычажной бесшкворневой
подвески) от вертикали соответственно в продольной и
поперечной
плоскостях. Угол поперечного наклона оси поворота о в
процессе
эксплуатации не регулируется. Остальные углы установки колес
при эксплуатации подлежат периодической проверке и регулировке.
Одновременно с указанными углами установки колес
производится также регулировка соотношения углов поворотов
колес.
Характерной особенностью передней подвески переднеприводных
автомобилей являются близкие к нулю или даже отрицательные
(на автомобилях АЗЛК) значения углов развала и схождения
колес. Расположение передних колес под такими углами
обеспечивает их параллельность при движении, когда на них
передается крутящий момент от двигателя автомобиля.
Благодаря компоновке узлов передней подвески переднеприводных
автомобилей обеспечивается отрицательное значение плеча
обката колес а (расстояние между центральной
плоскостью вращения колеса и осью его поворота в месте
пересечения с дорогой),
что повышает
безопасность при торможении автомобиля.
В отличие от переднеприводных автомобилей подвеска передних
колес автомобилей с классической схемой компоновки имеет
положительное значение углов развала и схождения колес, а
также
плеча обката колеса.
Передняя подвеска автомобиля ВАЗ-2106
(рис. 2) состоит
из поворотной стойки с осью ступицы 6, нижнего 36 и верхнего
13 рычагов, верхне-
|
|
|
|
|
|
|
Лист |
|
|
|
|
|
10 |
Изм. |
Лист |
№ документа |
Подпись |
Дата |
го шарового шарнира, нижней шаровой
опоры, винтовой пружины 38, амор-тизатора 40, буфера 15 и
стабилизатора поперечной устойчивости со штангой 33.
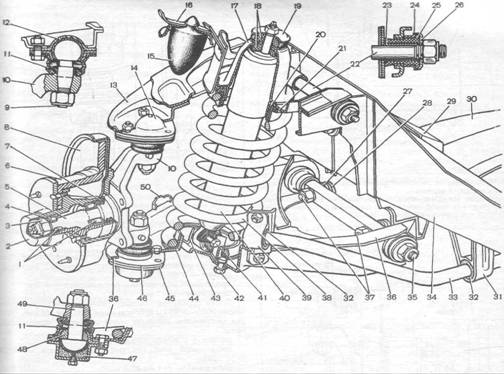
Рис. 2. Передняя подвеска:
1-подшипники ступицы переднего колеса; 2-колпак ступицы;
3-регулировоч-ная гайка; 4-шайба; 5-цапфа поворотного
кулака; 6-ступица колеса;
7-саль-ник;
8-тормозной диск; 9-шаровой палец верхней опоры;
10-поворотный ку-лак; 11-защитный чехол шарового пальца; 12-подшипник
верхней опоры; 13-верхний рычаг подвески; 14-корпус
подшипника верхней опоры; 15-буфер хода сжатия; 16-кронштейн
буфера хода сжатия;
17-опорный стакан амор-тизатора; 18-подушки крепления
амортизатора; 19-шайба подушки; 20-изо-лирующая прокладка
пружины подвески; 21-верхняя опорная чашка пружины подвески;
22-ось верхнего рычага подвески; 23-внутренняя втулка
шарнира; 24-наружная
втулка шарнира; 25-резиновая втулка шарнира; 26-опорная
шайба; 27-28-регулировочные шайбы; 29-кронштейн крепления
поперечины
к лонжерону кузова; 30-поперечина передней подвески;
31-кронштейн крепления штанги стабилизатора; 32-подушка
штанги стабилизатор;
33-штан-га стабилизатора; 34-лонжерон кузова; 35-ось нижнего
рычага; 36-нижний рычаг подвески; 37-болты крепления оси
нижнего рычага;
38-пружина под-вески; 39-обойма крепления штанги
стабилизатора; 40-амортизатор; 41-болт крепления
амортизатора; 42-гайка крепления кронштейна амортизатора к
рычагу подвески; 43-кронштейн крепления амортизатора к
нижнему рычагу подвески; 44-нижняя опорная чашка пружины
подвески; 45-обойма вкладыша нижней опоры; 46-корпус
подшипника нижней опоры; 47-вкладыш обоймы шарового пальца;
48-подшипник
нижней опоры; 49- шаровой палец; 50-ограничитель поворота
передних колес |
|
|
|
|
|
|
Лист |
|
|
|
|
|
11 |
Изм. |
Лист |
№ документа |
Подпись |
Дата |
Нижний рычаг
внутренними концами соединен шарнирно с
концами оси закрепленными болтами 37 на поперечине. Под болтами
установлены регулировочные прокладки (шайбы) 27-28, с помощью
которых регулируют углы продольного наклона оси поворота
и развала колес.
Верхний рычаг
внутренними концами соединен с верхней
осью.
Поворотная стойка
через шаровые шарниры, закрытые снаружи резиновыми чехлами,
соединяется с наружными кожухами
обоих рычагов.
Пружина
установлена между верхней опорной чашкой 21 и
нижним рычагом, опираясь снизу на опорную чашку.
Амортизатор
установлен следующим образом: нижним ушком
его корпус соединен с кронштейном 43, а верхний конец штока
амортизатора закреплен на двух резиновых подушках при
помощи гайки в опорном стакане кузова 17. Устроен и
работает амортизатор
аналогично рассмотренной выше амортизаторной стойке
переднеприводных автомобилей.
Ход колеса вверх и предельное сжатие пружины подвески
ограничиваются буфером, закрепленным на кузове над верхним
рычагом.
Ход колеса вниз ограничивают буферные втулки на штоке
передних амортизаторов.
Стабилизатор поперечной устойчивости
ограничивает боковой
крен и
поперечные колебания кузова. Стабилизатор своей средней
частью установлен в кронштейнах на резиновых втулках, а загнутые
концы его закреплены на нижних рычагах через резиновые
подушки обоймами.
Ступица колеса 6
установлена на цапфе поворотного кулака 5
на двух роликовых конических подшипниках, которые поджимаются
гайкой 3. Гайка стопорится путем накернивания и вдавливания
ее кромки в паз на цапфе поворотного кулака.
|
|
|
|
|
|
|
Лист |
|
|
|
|
|
12 |
Изм. |
Лист |
№ документа |
Подпись |
Дата |
3.
Техническое обслуживание и ремонт передней подвески.
3.1. Определение
состояния деталей передней подвески.
При ТО – 1, ТО – 2, а также
при ремонте следует обязательно проверять состояние защитных
чехлов шаровых шарниров подвески, обращая особое внимание на
отсутствие механических повреждений чехлов. Выясняют, нет ли
на деталях подвески трещин или следов задевания о дорожные
препятствия или кузов, деформаций поворотного кулака, оси
нижнего рычага, рычагов подвески, поперечины и элементов
передка кузова, а также проверяют зазор в верхнем шаровом
шарнире и состояние нижнего шарового шарнира.
Деформация оси нижнего
рычага
определяется осмотром.
Деформация поперечины
передней подвески
проверяется в следующем
порядке:
- отвернуть гайки крепления
осей нижних рычагов так, чтобы в полученный зазор между
дистанционной шайбой 28 (рис.2) и привалочной
поверхностью поперечины поместилась ножка штангенциркуля
вплотную к стержню переднего болта;
- замерить длину поперечины
между плоскостями установки осей нижних рычагов (левого и
правого) в зоне передних болтов. Расстояние должно быть
равно 611±1 мм.
Если поперечина
деформирована так, что углы установки колес не поддаются
регулировке, необходимо заменить поперечину.
Состояние
резинометаллических шарниров
проверяют в следующем
порядке:
- убедиться в отсутствии
деформации рычагов подвески оси нижнего рычага, поперечины,
а затем вывесить передние колеса автомобиля; |
|
|
|
|
|
|
Лист |
|
|
|
|
|
13 |
Изм. |
Лист |
№ документа |
Подпись |
Дата |
- замерить радиальное
смещение А (рис.3) наружной втулки 2 относительно внутренней
втулки 6 и расстояние В между наружной шайбой 5 и внешним
торцом наружной втулки 2.
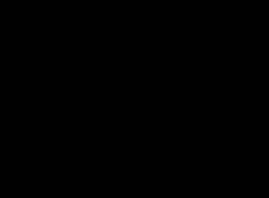
Рис. 3. Проверка состояния
резинометаллического шарнира рычага передней подвески:
1 – резиновая втулка
шарнира; 2 – наружная втулка шарнира; 3 – гайка крепления
оси рычага подвески; 4 – ось рычага; 5 – упорная шайба
шарнира;
6 – внутренняя втулка
шарнира
Резинометаллические шарниры
подлежат замене:
- при невозможности
дальнейшей регулировки развала колес (когда удалены все
шайбы из-под оси нижнего рычага);
- при разрывах и
одностороннем «выпучивании» резины;
- если радиальное смещение А
превышает 2,5 мм;
- если размер В не
укладывается в пределы 3-7,5 мм для нижнего рычага, 1,5-5 мм
для верхнего рычага.
Если размер В выходит за
указанные пределы, проверяют правильность запрессовки
резинометаллического шарнира в гнездо рычага.
Зазор в верхних шаровых
шарнирах
проверяют с помощью приспособления в следующем порядке:
- установить автомобиль на
ровной горизонтальной площадке с твердым покрытием, поднять
правую переднюю часть автомобиля и снять колесо;
- подставить под нижний
шаровой шарнир деревянную колодку 10 |
|
|
|
|
|
|
Лист |
|
|
|
|
|
14 |
Изм. |
Лист |
№ документа |
Подпись |
Дата |
(рис 4.) высотой 190 мм и
опустить на нее автомобиль;
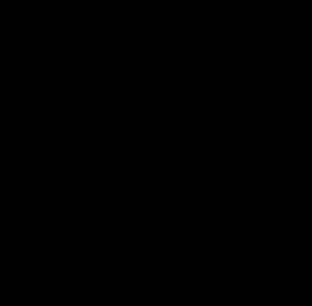
Рис. 4. Замер зазора в
верхнем шаровом шарнире приспособлением (тормоз условно не
показан):
1 – динамометрический ключ;
2 – защитный кожух тормоза; 3 – рычажок; 4 – винт; 5 –
удлинитель индикатора; 6 – болт; 7 – индикатор; 8 –
основание; 9 – втулка; 10 – колодка; 11 – ось; 12 – пружина;
13 – шайба; 14 – шплинт; 15 – ступица колеса; 16 – кронштейн
- установить втулку 9 на
гайку ближайшего к кожуху болта крепления верхнего шарнира,
надеть на втулку основание 8 и слегка закрепить его винтом
4;
- передвигая приспособление,
установить рычажок 3 в вертикальное положение так, чтобы его
нижний конец упирался в защитный кожух 2 тормоза, и затянуть
винт 4;
- установить в стойку
основания 8 индикатор 7 до упора его ножки в рычажок 3 с
натягом 2-3 мм и затянуть болт 6;
- прикрепить кронштейн 16 к
ступице 15 двумя болтами крепления колеса, надеть
динамометрический ключ 1 на шестигранную головку оси
кронштейна 16 и моментом 196 Н.м (20кгс.м),
повернуть ключ к автомобилю и от него, оба показания
индикатора суммируют; |
|
|
|
|
|
|
Лист |
|
|
|
|
|
15 |
Изм. |
Лист |
№ документа |
Подпись |
Дата |
- суммарные показания
индикатора не должны превышать 0,8 мм;
- повторить операции для
подвески левого переднего колеса.
Состояние нижних шаровых
шарниров
проверяется в следующем порядке:
- установить автомобиль на
ровной горизонтальной площадке с твердым покрытием и, подняв
правую переднюю часть автомобиля, снять колесо;
- поставить под ступицу 1
(рис.5) деревянную колодку высотой 280 мм и опустить на нее
автомобиль, очистить нижнюю часть шарнира от пыли и грязи и
вывернуть коническую пробку;
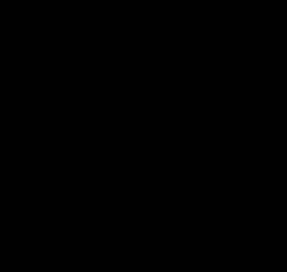
Рис. 5. Схема проверки
нижних шаровых шарниров:
1 – ступица колеса; 2 –
нижний рычаг; 3 – нижний шаровой шарнир; 4 –
штан-генциркуль; 5 – деревянная колодка
- замерить глубиномером
штангенциркуля 4 расстояние «h»,
как показано на схеме;
- повторить операции для
подвески левого переднего колеса.
Если
h≥11,3
мм, необходимо снять шарнир с автомобиля и тщательно
осмотреть. На корпусе шарнира не должно быть трещин, а в
смазке – грязи. При наличии грязи в смазке, трещин на
корпусе шарнира, а также при
h≥11,8
мм – заменить шарнир. |
|
|
|
|
|
|
Лист |
|
|
|
|
|
16 |
Изм. |
Лист |
№ документа |
Подпись |
Дата |
3.2.
Проверка и регулировка углов установки передних
колес.
Проверка и регулировка углов
установки передних колес выполняется на специальных стендах
в соответствии с инструкцией на стенд.
ПРЕДУПРЕЖДЕНИЕ. Проверка
углов установки колес обязательна, если производится замена
или ремонт деталей подвески, которые могут повлечь за собой
изменение углов установки колес.
У нового автомобиля (до
первого технического обслуживания) углы установки колес
имеют следующие значения:
Развал – 0о30´ ;
Продольный угол наклона оси
поворота – 4о
Схождение - 1 7
мм.
После проведения первого
технического обслуживания (через 2 000 – 3 000 км пробега) и
при дальнейшей эксплуатации автомобиля значение углов
установки колес должно быть:
Развал – 0о30'±20'
без нагрузкой (0о5'±20' с нагрузкой);
Продольный угол наклона оси
поворота – 4о±30' (3о30'±30');
Схождение - 2 4
мм (3 5
мм).
Разница в продольных углах
наклона осей поворота правого и левого колес не должна
превышать 0о30'.
Перед регулировкой углов
установки колес проверяют:
- давление воздуха в шинах;
- осевой зазор в подшипниках
ступиц передних колес;
- исправность амортизаторов
(отсутствие заклинивания штока);
- радиальное и осевое биение
шин;
- зазор в верхних шаровых
шарнирах подвески;
- свободный ход рулевого
колеса.
Обнаруженные неисправности
устранить и произвести необходимые регулировки. |
|
|
|
|
|
|
Лист |
|
|
|
|
|
17 |
Изм. |
Лист |
№ документа |
Подпись |
Дата |
Контроль и регулировку углов
установки колес можно проводить как на груженом автомобиле,
так и на ненагруженном, однако контроль углов на груженом
автомобиле дает более точные результаты. Поэтому в
ответственных случаях рекомендуется проводить контроль и
установку углов на автомобиле под статической нагрузкой
3 136 Н (320 кгс), что соответствует приблизительно весу
четырех человек и грузу 40 кг в багажнике.
Автомобиль нагружается или
специальными грузами, подвешиваемыми к днищу кузова, или
балластом (280 кг), размещенным на подушках сидений и в
багажнике (40 кг). Передние сиденья должны находиться в
среднем положении их продольного хода. Груз в багажнике
размещается равномерно. Недостаток топлива компенсируется
грузом, располагаемым на правой стороне площади багажника.
После установки автомобиля на стенд непосредственно
перед контролем углов "прожимают" подвеску автомобиля,
прикладывая 2-3 раза усилие в 392-490 Н (40-50 кгс), направленное
сверху вниз, сначала на задний, а потом на передний
бампер. При этом колеса автомобиля должны располагаться
параллельно продольной оси автомобиля.
Очередность проверки и регулировки углов установки
колес следующая:
1)
угол продольного наклона оси поворота;
2)
угол развала;
3)
схождение.
Угол продольного наклона оси поворота.
Если при проверке величина угла не соответствует данным,
приведенным выше, необходимо изменить количество регулировочных
шайб 27 и 28 (рис. 2), установленных между осью нижнего
рычага и поперечиной.
Для регулировки угла продольного наклона для поворота:
необходимо
ослабить гайки крепления оси рычага к поперечине и изменить
количество регулировочных шайб под болтами для получения
правильного угла продольного наклона оси поворота
колес; |
|
|
|
|
|
|
Лист |
|
|
|
|
|
18 |
Изм. |
Лист |
№ документа |
Подпись |
Дата |
затянуть
гайки динамометрическим ключом и проверить продольный угол
наклона оси поворота.
ПРИМЕЧАНИЕ. При регулировке
углов установки передних колес допускается применение
П-образных регулировочных прокладок, которые должны быть
установлены прорезью вниз.
Угол развала передних колес.
Если
угол
развала отличается от нормы, регулируют его, изменяя
количество регулировочных шайб 27 и 28 (рис.2),
установленных между осью рычага и поперечиной.
Для увеличения угла развала снимают с обоих болтов одинаковое
количество шайб, а для уменьшения — добавляют.
Схождение передних колес.
Если величина
схождения отличается от нормы, ослабляют
стяжные хомутики боковых тяг и ключом поворачивают
обе муфты на одинаковую величину в противоположных
направлениях; таким образом муфты наворачиваются или
отворачиваются и изменяют
длину боковых тяг.
Выполнив регулировку, установить стяжные хомутики прорезью
горизонтально с отклонением вверх или вниз не
более 60° и в таком положении затянуть их. При затянутых
гайках кромки прорезей стяжных хомутиков не должны соприкасаться.
Проверка и регулировка зазора в подшипниках ступицы
переднего колеса.
Для проверки зазора поднимают переднюю часть автомобиля,
опирают
ее на подставки и снимают передние колеса.
Под болт крепления колеса устанавливают приспособление
(рис. 6). Упирают ножку индикатора в торец
воротного кулака при нулевом положении стрелки и, перемещая
ступицу вдоль оси поворотного кулака, замеряют величину
перемещения (зазора) по индикатору.
Если зазор больше 0,15 мм, регулируют его в следующем порядке:
|
|
|
|
|
|
|
Лист |
|
|
|
|
|
19 |
Изм. |
Лист |
№ документа |
Подпись |
Дата |
отвернуть
регулировочную гайку с цапфы поворотного кулака;
установить новую или бывшую в употреблении, но на другом автомобиле
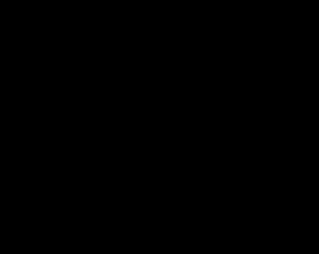
Рис. 6. Проверка осевого
зазора подшипников ступицы переднего колеса приспособлением:
1 – индикатор; 2 – болт; 3 –
кронштейн; 4 – ступица колеса.
гайку,
затянуть ее моментом 19,6 Н.м (2 кгс.м),
одновременно поворачивая
ступицу в обоих направлениях два-три
раза для самоустановки роликов подшипников;
ослабить регулировочную гайку и снова затянуть ее мо-16
8 Н-м (0,7 кгс.м);
на шайбе
сделать метку В (рис.7), затем отпустить
гайку так, чтобы кромка
А немного не дошла до метки В;
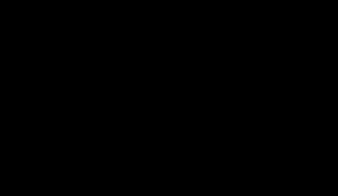
Рис. 7. Схема регулировки
подшипников ступицы переднего колеса:
А – кромка гайки; Б – метка
на шайбе |
|
|
|
|
|
|
Лист |
|
|
|
|
|
20 |
Изм. |
Лист |
№ документа |
Подпись |
Дата |
застопорить гайку в этом положении, вдавливая лунки на шейке
гайки
в пазы на конце оси поворотного кулака.
После регулировки зазор в подшипнике должен быть в пределах
0,02-0,08 мм. При регулировке зазора следует учитывать, что
направление резьбы на левой цапфе поворотного кулака правое,
а на правой цапфе – левое.
Замена смазки в подшипниках ступиц передних колес.
Для замены смазки:
снимают декоративные колпаки и ослабляют болты крепления
колес;
поднимают переднюю часть автомобиля и опирают ее на
подставки, отворачивают болты и снимают колеса;
отогнув лепестки стопорных пластина, выворачивают болты
крепления суппорта тормоза; снимают суппорт и отводят его в
сторону, не отсоединяя шланг подвода жидкости, чтобы в
систему гидропривода тормозов не попали воздух и грязь;
суппорт не должен висеть на трубопроводах;
съемником (рис.8) снимают колпак ступицы переднего колеса;
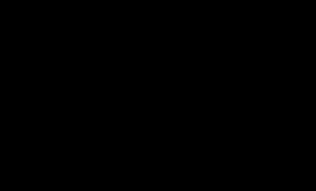
Рис.8.Снятие колпака ступицы
колеса съемником.
отворачивают регулировочную
гайку, снимают шайбу и съемником спрессовывают ступицу в
сборе с тормозным диском, подшипниками и сальником; снимают
ступицу с поворотного кулака;
выпрессовав сальник ступицы, снимают дистанционное и
внутреннее кольцо внутреннего подшипника с роликами в сборе; |
|
|
|
|
|
|
Лист |
|
|
|
|
|
21 |
Изм. |
Лист |
№ документа |
Подпись |
Дата |
промывают внутреннюю полость
ступицы и подшипники керосином;
перед установкой сепараторы
подшипников заполняют смазкой ЛИТОЛ-24. Пространство между
наружными кольцами подшипников по внутренней поверхности
ступицы равномерно заполняют этой же смазкой в количестве 40
г. В колпак ступицы, перед его установкой, закладывают 25 г
смазки;
устанавливают внутреннее
колесо внутреннего подшипника с роликами в сборе и
дистанционное колесо в ступицу;
запрессовывают в ступицу
новый сальник, используя оправку;
осторожно, чтобы не
повредить сальник, устанавливают ступицу в сборе с тормозным
диском на поворотный кулак, затем внутреннее колесо
наружного подшипника, шайбу, и заворачивают новую или бывшую
в употреблении, но на другом автомобиле, гайку;
регулируют зазор в
подшипниках ступицы.
Балансировка колес.
Колеса
балансируют на специальных стендах, согласно правилам,
описанным в инструкциях, прилагаемых к стендам. После
балансировки предельно-допустимый дисбаланс колеса в сборе с
шиной равен 24,5 Н.мм (2 600 г.мм).
Эта величина дисбаланса соответствует массе грузика около 15
г. Дисбаланс колеса устраняется балансировочными грузиками,
которые удерживаются на ободе специальными пружинами. Не
рекомендуется превышать массу грузиков в каждой плоскости
балансирования более 80 г.
Снятие и установка
передней подвески.
Установить автомобиль на
подъемник или смотровую канаву; удерживая ключом конец штока
за лыски, отсоединить верхний конец амортизатора. Снять
передние колеса.
Разогнув стопорные пластины,
отворачивают болты крепления суппорта к кронштейну. Отводят
суппорт в сторону и закрепляют его так, чтобы он висел на
шлангах. Снимают амортизаторы с кронштейнами. |
|
|
|
|
|
|
Лист |
|
|
|
|
|
22 |
Изм. |
Лист |
№ документа |
Подпись |
Дата |
Отсоединяют конца штанги
стабилизатора поперечной устойчивости от нижних рычагов
подвески.
Съемником выпрессовывают
пальцы из отверстий рычагов и отводят рулевые тяги в
сторону.
Вставить винт 2 (рис. 9)
приспособления в отверстие верхней опоры пружины подвески,
затем снизу надеть на виток пружины 1 и на винт 2 опорную
тарелку 3 и закрепить ее на пружине зажимом. Снизу на винт
навернуть гайку так, чтобы фиксатор гайки зашел в гнездо
тарелки 3. Вращая ключом винт 2, сжать пружину подвески до
полной разгрузки рычагов подвески.
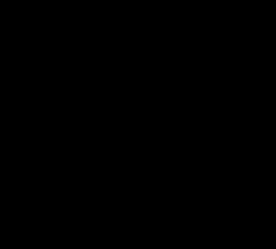
Рис.9. Сжатие пружины
приспособлением:
1 – пружина подвески; 2 –
винт приспособления; 3 – опорная тарелка
Вынуть ось верхнего рычага и отсоединить его от кузова.
Отсоединить ось нижнего рычага от поперечины и снять узел
подвески с автомобиля.
Снять пружину, плавно разгрузив ее, убрать приспособление
и повторить операции для другого узла подвески.
ПРИМЕЧАНИЕ. Снимая узлы подвески, необходимо отметить
количество и расположение шайб между осью нижнего рычага и
поперечиной, а также регулировочных пластин между
поперечиной и лонжеронами кузова, чтобы при установке узлов
поставить
эти шайбы и пластины на прежнее место. |
|
|
|
|
|
|
Лист |
|
|
|
|
|
23 |
Изм. |
Лист |
№ документа |
Подпись |
Дата |
Снять брызговик двигателя и штангу стабилизатора.
Поддерживая двигатель траверсой (рис.10) или
талью, снять поперечину.
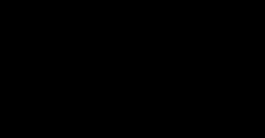
Рис. 10. Установка траверсы
для поддержания двигателя при снятии поперечины передней
подвески
Узлы и детали подвески устанавливают в порядке, обратном
снятию. На передней и задней подвесках устанавливают
пружины только группы А (маркируются желтой красна наружной
поверхности витков). В исключительных случаях
допускается установка на задней подвеске пружин группы
В (маркируются зеленой краской).
Для предупреждения неправильного распределения усилий
в резинометаллических шарнирах затягивают гайки и оси
рычагов в следующем порядке:
установить автомобиль на ровной площадке и поставить колеса
параллельно оси автомобиля;
нагрузить автомобиль нагрузкой 3136 Н (320 кгс) (четыре
человека и 40 кг в багажнике);
в этих условиях затянуть динамометрическим ключом крепления
осей верхнего, а затем нижнего рычагов и крепления оси
нижнего рычага к поперечине.
Проверить и отрегулировать углы установки передних колес.
Разборка и сборка узлов подвески.
Разборка.
Если при ремонте подвески необходима полная разборка
ее узлов, то начинают ее непосредственно на автомобиле,
перед тем как сжать пружину подвески. Для этого: |
|
|
|
|
|
|
Лист |
|
|
|
|
|
24 |
Изм. |
Лист |
№ документа |
Подпись |
Дата |
необходимо отогнуть лепестки стопорных пластин, вывернуть
болты крепления суппорта, отведя его в сторону, и закрепить
суппорт
так, чтобы он не висел на шлангах;
съемником
(рис. 8) снимают колпак ступицы
переднего колеса;
отворачивают регулировочную гайку подшипников ступицы,
снимают шайбу и съемником (рис. 11) снимают ступицу
в сборе с подшипниками, сальником и тормозным диском;
снимают внутреннее кольцо внутреннего подшипника с
поворотного кулака.
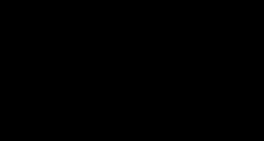
Рис. 11. Снятие ступицы
переднего колеса съемником:
1 – ступица колеса; 2 –
съемник
Дальнейшую разборку проводят после снятия с автомобиля
узла подвески, закрепив его на верстаке, и, действуя в
следующем порядке:
отвернуть все гайки 1 (рис. 12), снять стопорные
пластины и рычаг поворотного кулака; при этом освобождаются
кронштейн 2 крепления тормозного суппорта и защитный
кожух 3 тормозного диска;
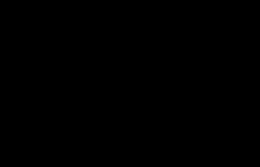
Рис. 12. Узел подвески
колеса, закрепленный на верстаке для разборки:
1 – гайки крепления
поворотного кулака, кронштейна крепления суппорта и
защитного кожуха к поворотному кулаку; 2 – кронштейн
крепления суппорта; 3 – защитный кожух тормозного диска |
|
|
|
|
|
|
Лист |
|
|
|
|
|
25 |
Изм. |
Лист |
№ документа |
Подпись |
Дата |
отвернуть гайку крепления пальца верхнего шарнира,
установить съемник (рис. 13) между пальцами
шаровых шарниров и, заворачивая болт съемника, выпрессовать
палец верхнего шарнира из поворотного кулака;
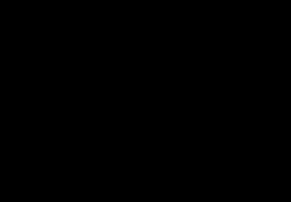
Рис.13. Отсоединение
верхнего рычага:
1 – поворотный кулак; 2 –
палец шарового шарнира;
3 – приспособление;
4 – болт
отвернуть гайку крепления пальца нижнего шарнира, установить
между пальцами гарнира и упором 2 (рис.14) съемник;
заворачивая болт съемника, выпрессовать палец и снять
передний рычаг с кулака.
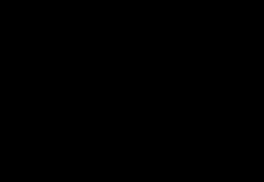
Рис.14. Отсоединение нижнего
рычага:
1 – поворотный кулак; 2 –
упор; 3 – приспособление;
4 – болт; 5 – палец шарового
шарнира
Сборку
узлов подвески проводят в последовательности,
обратной разборке, при этом:
подшипники ступиц передних колес заполняют смазкой
ЛИТОЛ-24, как указано в разделе "Замена смазки в подшипниках
ступиц передних колес"; |
|
|
|
|
|
|
Лист |
|
|
|
|
|
26 |
Изм. |
Лист |
№ документа |
Подпись |
Дата |
перед сборкой шаровых шарниров рычагов подвески закладывают
в защитные чехлы смазку ШРБ-4 или ЛИТОЛ-24 в
количестве, равном 1/3 объема чехла в свободном состоянии;
гайки и болты крепления узлов и деталей подвески затягивают;
после сборки подвески и установки ее на автомобиль
следует "обмять" элементы подвески, совершив пробег 15— 20
км, после которого обязательно проверить и, при необходимости,
отрегулировать углы установки колес.
Проверка технического состояния и ремонт.
Рычаги подвески.
Деформация верхних и нижних рычагов
определяется на приспособлении.
Нижний рычаг устанавливайте так, чтобы оправка 1
(рис.
15)
для центровки сочленялась с конусом пальца
шарового шарнира рычага, а установочные пальцы приспособления
входили в отверстия 3 оси рычага.
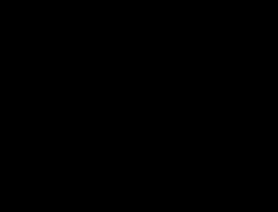
Рис. 15. Проверка левого
нижнего рычага:
1 – оправка для центровки
шарового шарнира; 2 – нижний рычаг; 3 – отверстие для
установочных пальцев приспособления; 4 – приспособление для
проверки рычагов
Оправка для центровки должна входить соответственно
в правое или центральное отверстие приспособления в зависимости
от того, какой рычаг проверяется, правый или левый.
Признаком деформации рычага является невозможно
введения без усилия пальцев приспособления в отверстия 3
оси рычага, а также плохое сочленение |
|
|
|
|
|
|
Лист |
|
|
|
|
|
27 |
Изм. |
Лист |
№ документа |
Подпись |
Дата |
оправки 1 с конусом
пальца шарового шарнира.
Верхний рычаг устанавливайте на приспособление (рис. 16)
в перевернутом положении так, чтобы оправка 2
центровки точно совпадала с хвостовиком пальца шарового
шарнира 1, а палец 4 проходил в отверстия резинометаллических
шарниров рычага.
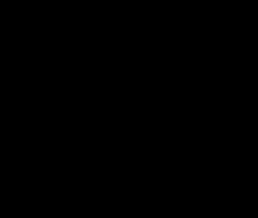
Рис. 16. Проверка левого
верхнего рычага:
1 – шаровой шарнир; 2 –
оправка для центровки шарового шарнира;
3 – верхний рычаг; 4 – палец
для центровки шарниров; 5 – приспособление
Величина деформации рычага определяется по трудности ввода
пальца 4 в отверстия шарниров рычагов и по плохому
сочленению конического гнезда оправки 2 с конической
поверхностью пальца шарового шарнира 1. Палец 4
должен входить в
отверстия шарниров без особого усилия.
При небольшой
деформации рычаги можно выправить, а при большой
— заменить.
Шаровые шарниры.
Необходимо убедиться в сохранности грязезащитных
чехлов шаровых шарниров. Разрывы, трещины, отслоения
резины от металлической арматуры, следы утечки смазки
недопустимы.
Проверить, нет ли износа рабочих поверхностей шаровых
шарниров, поворачивая вручную шаровой палец. Свободный
ход пальца или его заедание недопустимы.
Более точная проверка состояния верхнего шарового шарнира
по величине радиального и осевого зазора проводится на
приспособлении.
Для |
|
|
|
|
|
|
Лист |
|
|
|
|
|
28 |
Изм. |
Лист |
№ документа |
Подпись |
Дата |
этого установить шаровой
шарнир 1 (рис. 17, а) в гнездо приспособления и
зажать его винтом.
Установить в кронштейн приспособления индикатор 2
так, чтобы его ножка упиралась в боковую поверхность
корпуса шарнира, а стрелка индикатора стояла на нуле.
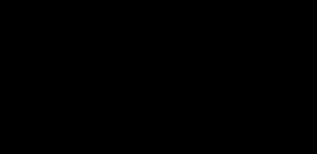
Рис. 17. Проверка верхнего
шарового шарнира на приспособлении:
а – схема проверки
радиального зазора; б – схема проверки осевого зазора;
1 – шаровой шарнир; 2 –
индикатор; 3 – динамометрический ключ;
4 – приспособление
Установить динамометрический ключ 3 в верхнее гнездо
приспособления и, приложив к нему момент 196 Н.м
(20 кгс.м)
в обе стороны, определить по индикатору суммарный радиальный
зазор в шаровом шарнире. Если он превышает 0,7
мм, шарнир заменить новым.
Аналогично проверяется осевой зазор в шаровом шарнире, предварительно
изменив его крепление в приспособлении,
как указано на рис. 17, Б. Осевой зазор в шарнире допускается
не более 0,7 мм.
Резинометаллические шарниры.
Признаки, при которых необходимо заменять
резинометаллические шарниры описаны в п. «Определение
состояния деталей передней подвески». Порядок замены
следующий:
Нижний
рычаг.
Установить его на оправку 3 (рис. 18)
и пуансоном пресса
нажать на ось 1 рычага до выпрессовки
шарнира 2 из отверстия. Для выпрессовки второго шарнира
перевернуть рычаг и повторить операцию.
|
|
|
|
|
|
|
Лист |
|
|
|
|
|
29 |
Изм. |
Лист |
№ документа |
Подпись |
Дата |
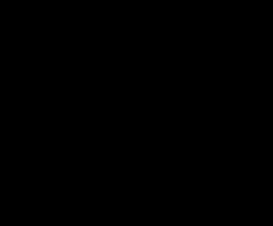
Рис. 18. Выпрессовка
шарниров нижнего рычага:
1 – ось рычага; 2 – шарнир
рычага; 3 – оправка
Запрессовку шарниров нижних рычагов выполняют
помощью распорной втулки (рис. 19), зажатой
тисках, и приспособления. Рычаг с осью 1 установите
на приспособление 2, наденьте на ось шарнир и запрессуйте
его в гнездо рычага при помощи приспособления 3.
Затем повторить вышеописанные операции для
запрессовки второго шарнира с другой стороны рычага.
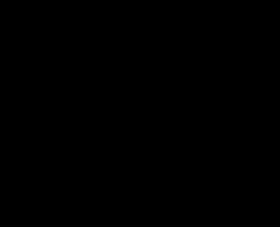
Рис.19. Запрессовка шарниров
нижнего рычага:
1 – ось рычага; 2 –
приспособление; 3 – приспособление
Верхний рычаг.
Для выпрессовки шарниров установить приспособление
(рис.20) на рычаге так, чтобы головка
винта приспособления была направлена внутрь. |
|
|
|
|
|
|
Лист |
|
|
|
|
|
30 |
Изм. |
Лист |
№ документа |
Подпись |
Дата |
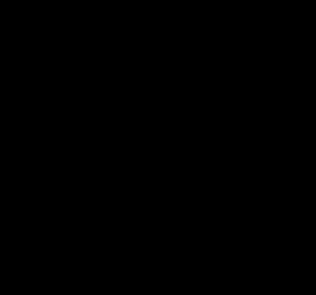
Рис.20. Выпрессовка шарниров
верхнего рычага:
1 – приспособление; 2-
шарнир
Заворачиванием винта
приспособления выпрессовать шарнир 2.
Для запрессовки вставить шарнир в гнездо рычага и установить
приспособление (рис.21) в комплекте
колпачком 3. Заворачивая винт приспособления, запрессовать
шарнир в гнездо рычага.
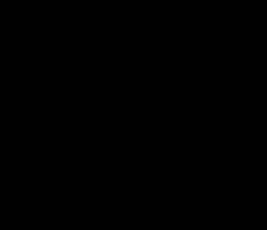
Рис.21. Запрессовка шарниров
верхнего рычага:
1 – приспособление; 2 –
шарнир; 3 – колпачок, применяемый вместе с приспособлением
|
|
|
|
|
|
|
Лист |
|
|
|
|
|
31 |
Изм. |
Лист |
№ документа |
Подпись |
Дата |
Поворотные кулаки.
Для проверки установить поворотный
кулак на калибре (рис.22), зажатом в тисках
так, чтобы поверхность его под сальник ступицы колеса
совпала с отверстием калибра.
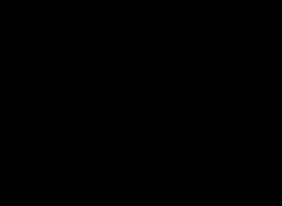
Рис.22. Проверка поворотного
кулака:
1 – поворотный кулак; 2 –
калибр
Ввести два боковых установочных пальца калибра
отверстия кулака. Если введение пальцев требует некоторого
усилия, значит кулак деформирован и его необходимо
заменить новым.
Пружины подвески.
Тщательно осмотреть пружины. Если будут обнаружены
деформации, которые могут стать причиной
нарушения работоспособности, заменить пружины новыми.
Трехкратно
обжав пружину до соприкосновения витков,
проверить ее упругость по контрольным точкам (см.
рис.23).
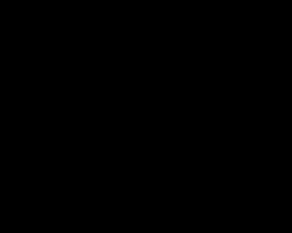
Рис.23. Основные данные для
проверки пружин передней подвески |
|
|
|
|
|
|
Лист |
|
|
|
|
|
32 |
Изм. |
Лист |
№ документа |
Подпись |
Дата |
Проверить техническое состояние изолирующих прокладок
и заменить их, если они имеют повреждения.
Штанга стабилизатора.
Проверить, не деформирована ли
штанга и находятся ли ее концы в одной плоскости; если
деформация незначительна, то выправить штангу; при значительной
деформации заменить штангу.
Провериь сохранность подушек в кронштейнах крепления
к кузову и к нижним рычагам подвески; при износе заменить
подушки.
Поперечина передней подвески.
Для проверки установить
поперечину на приспособлении (рис. 24) так,
чтобы штыри
совпадали с отверстиями 1 поперечины.
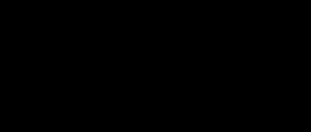
Рис.24. Проверка поперечины
передней подвески:
1 – отверстия на поперечине
под установочные штыри приспособления; 2 – поперечина; 3 –
контрольные втулки приспособления; 4 – приспособление; 5 –
контрольные отверстия болтов на поперечине
Навернуть на концы двух болтов поперечины контрольные
втулки 3 приспособления.
Отверстия 5 приспособления и находящиеся против них
болты поперечины должны быть соосны.
Признаки деформации поперечины — невозможность
ввода без усилия штырей приспособления в отверстия поперечины,
несоосность болтов поперечины с втулками 3 приспособления.
При выявлении деформации, которая не может быть устранена
правкой, заменить поперечину. |
|
|
|
|
|
|
Лист |
|
|
|
|
|
33 |
Изм. |
Лист |
№ документа |
Подпись |
Дата |
Замена резинометаллических шарниров рычагов
на автомобиле.
Необходимость замены резинометаллических шарниров
определяют по признакам, указанным выше, в главе "Определение
состояния деталей передней подвески".
Заменять шарниры можно как непосредственно на автомобиле,
так и на рычагах, снятых с автомобиля (описано в главе
"Проверка технического состояния и ремонт").
Замена резинометаллических шарниров нижних рычагов
производится в следующем порядке:
поставит автомобиль на смотровую канаву или подъемник и
вывесить переднюю часть автомобиля со стороны, где
будет производиться замена. Снять колесо;
отвернув гайку, выпрессовать палец шарового шарнире рулевой
тяги съемником и отвести свободный конец
боковой тяги назад;
отвернуть гайки крепления нижнего рычага подвески и
оси и снять шайбы с обоих концов оси;
установите стакан 3 (рис.25) приспособления
на полку рычага 4 и навернуть винт 1 на конец
оси 6;
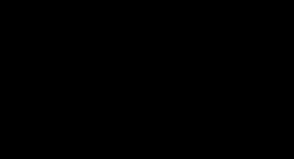
Рис.25. Схема выпрессовки
шарнира нижнего рычага с помощью приспособления:
1 – винт; 2 – гайка; 3 –
стакан; 4 – нижний рычаг; 5 – шарнир; 6 – ось нижнего рычага
удерживая винт 1 воротком, и, вращая гайку 2, сдвинуть проушину
рычага с наружной обоймы шарнира. Снять приспособление
и выпрессован- |
|
|
|
|
|
|
Лист |
|
|
|
|
|
34 |
Изм. |
Лист |
№ документа |
Подпись |
Дата |
ный шарнир 5 с оси рычага;
придавая ломиком или монтажной лопаткой проушине рычага
положение, концентричное с осью рычага, вставить новый
шарнир в отверстие проушины рычага и надеть на ось;
надеть на конец оси кольцо 2 (рис.26) приспособление
и вставить
упор 5 между полкой 4 и ближайшей
гайкой
крепления оси к поперечине передней подвески;
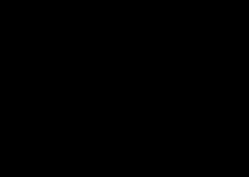
Рис.26. Схема запрессовки
шарнира нижнего рычага с помощью приспособления:
1 – гайка; 2 – кольцо; 3 –
шарнир; 4 – нижний рычаг; 5 – упор; 6 – ось нижнего рычага
вращая гайку 1, и, придерживая упор 5, запрессовать новый
шарнир 3 в проушину рычага. Снять приспособление, установить
шайбу и гайку крепления рычага к оси. Гайку не затягивать.
Аналогично заменяются другие резинометаллические шарниры
нижних рычагов подвески.
После замены шарниров соединить рулевую тягу с рычагом
поворотного кулака, затянуть и зашплинтовать гайку шарового
пальца рулевой тяги, установить и закрепить колесо.
Замену резинометаллических шарниров верхних рычагов
подвески
производят с помощью приспособления
таким же способом, как и на снятых рычагах (см. рис.20. и 21),
в следующем порядке: |
|
|
|
|
|
|
Лист |
|
|
|
|
|
35 |
Изм. |
Лист |
№ документа |
Подпись |
Дата |
поставить автомобиль на смотровую канаву или подъемник;
вывесить домкратом переднюю часть автомобиля со стороны,
где будет производиться замена. Снять колесо;
отвернуть гайку оси верхнего рычага и, вынув ось, развернуть
рычаг проушинами наружу;
установить на рычаге стакан 3 (рис.27) приспособления
с гайкой 2 и болтом 1 головкой внутрь рычага. Вращая
гайку 2, выпрессовать шарнир, снять приспособление
и шарнир;
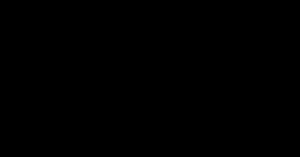
Рис.27. Схема выпрессовки
шарнира верхнего рычага:
1 – болт; 2 – гайка; 3 –
стакан приспособления; 4 – шарнир;
5 – верхний рычаг
вставить новый шарнир в проушину рычага, установить
приспособление А.47046 так, чтобы головка болта 1 (рис.28)
была направлена наружу и под головкой находилось кольцо
2 приспособления. Вращая гайку 6, запрессовать
шарнир и снять приспособление.
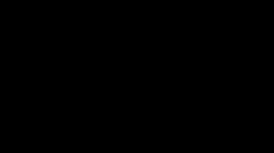
Рис.28. Схема запрессовки
шарнира верхнего рычага:
1 – болт; 2 – кольцо
приспособления; 3 – шарнир; 4 – верхний рычаг; 5 – стакана
приспособления; 6 – гайка |
|
|
|
|
|
|
Лист |
|
|
|
|
|
36 |
Изм. |
Лист |
№ документа |
Подпись |
Дата |
Аналогично заменяются другие шарниры верхних рычагов
передней подвески.
После замены шарниров повернуть верхний рычаг проушинами
к стойке передка, надвинуть его на стойку, вставить ось
верхнего рычага, установить шайбу и гайку оси, не затягивая
ее окончательно.
Установить колеса, опустить автомобиль и затянуть гайки осей
рычагов. Перед затягиванием гаек выполнить все операции,
описанные раньше (см. «Установка подвески на автомобиль»).
После замены резинометаллических шарниров совершают пробный
выезд на 15-20 км и в обязательном порядке проверяют, а при
необходимости, регулируют углы установки передних колес.
3.3.
Инструменты и приспособления для ТО и ремонта
передней подвески.
Приспособления;
штангенциркуль;
деревянная колодка;
ключи;
съемники;
оправка;
траверса;
распорная втулка;
приспособление;
калибр;
ломик или монтажная лопатка. |
|
|
|
|
|
|
Лист |
|
|
|
|
|
37 |
Изм. |
Лист |
№ документа |
Подпись |
Дата |
5.Техника безопасности и
пожарная безопасность при проведении технического
обслуживания и ремонта.
Помещение, где проводятся
ремонтные работы, должно хорошо проветриваться, дверь или
ворота – легко открываться как изнутри, так и снаружи.
Проход к выходу всегда
держите свободным.
При работе двигателя
(особенно на режимах прогрева) выделяется оксид углерода
(СО) – ядовитый газ без цвета и запаха. Отравиться оксидом
углерода (угарным газом) можно даже в открытом гараже,
поэтому перед пуском двигателя обеспечьте отвод отработавших
газов за пределы гаража. Например, шлангом, надев его на
выпускную трубу. При отсутствии принудительной вытяжки
пускать двигатель можно только на короткое время. При этом
система выпуска и ее соединение со шлангом должны быть
герметичны!
При ремонте системы питания
двигателя будьте осторожны: бензин может попасть на горячий
выпускной коллектор и вызвать пожар. Не включайте (и не
выключайте) электроприборы автомобиля, если поблизости
пролился бензин – проскочившая искра (даже при снятии
«минусовой» клеммы с аккумулятора) может вызвать взрыв.
Во время сварочных работ
держите под рукой ведро с водой, огне6тушитель (лучше
углекислотный). Перед этим отключите все электронные блоки
управления и аккумуляторную батарею от бортовой сети
автомобиля, а «массовый» контакт сварочного провода
располагайте как можно ближе к месту сварки. Проследите за
тем, чтобы ток не проходил через подвижные (подшипники,
шаровые опоры) или резьбовые соединения – они могут быть
повреждены. При ремонте цепей электрооборудования или при
риске их повреждения (сварка, рихтовка вблизи жгутов
проводов) отключайте клемму «минус» аккумуляторной батареи.
|
|
|
|
|
|
|
Лист |
|
|
|
|
|
38 |
Изм. |
Лист |
№ документа |
Подпись |
Дата |
Обслуживая бесконтактную
систему зажигания, не касайтесь высоковольтных проводов на
работающем или при его пуске. При проверке системы зажигания
«на искру» закрепите высоковольтный провод вблизи «массы»
изолентой, прищепкой, но не держите руками. Если требуется
отключить один из цилиндров на работающем двигателе,
замкните отверткой или отрезком подходящего провода
высоковольтный вывод на «массу». При этом шунтирующий провод
сначала надежно закрепите на «массе», а затем уже подносите
к наконечнику высоковольтного провода (лучше не касаться его
руками).
Если вы предпочитаете для
отключения цилиндров отсоединять высоковольтные провода (а
это может привести к прогару изоляции катушки зажигания,
бегунка и крышки распределителя), то лучше отсоединить их не
от свечей, а от распределителя зажигания – так намного
меньше вероятность получить удар током.
Чтобы во время работы не
повредить руки, надевайте перчатки (лучше кожаные). Для
защиты глаз надевайте специальные очки с боковыми щитками.
Электросварочные работы
выполняйте в плотной одежде (лучше брезентовой), застегнув
рукава и воротник.
По возможности пользуйтесь
ромбическими или гидравлическими домкратами вместо шатунных
– они более устойчивы и надежны. Не применяйте неисправный
инструмент: рожковые ключи с «раскрывшимся» зевом или
смятыми губками, отвертки со скругленным, скрученным шлицем
или неправильно заточенные, пассатижи с плохо закрепленными
пластмассовыми ручками, молотки с незафиксированной
рукояткой и т.п.
Перед подъемом автомобиля на
домкрате или подъемнике убедитесь, что соответствующие
силовые элементы кузова (усилители пола, пороги) достаточно
прочны. Используйте для подъема автомобиля только штатные
точки опоры. Запрещается вывешивать автомобиль на двух или
более домкратах – используйте исправные подставки
промышленного изготовлении («треноги») и надежные упоры под
колеса. |
|
|
|
|
|
|
Лист |
|
|
|
|
|
39 |
Изм. |
Лист |
№ документа |
Подпись |
Дата |
Запрещается нагружать или
разгружать автомобиль, стоящий на домкрате, садиться в него,
снимать или устанавливать двигатель, если под автомобилем
находятся люди. При ремонте автомобиля со снятым двигателем
или мостом учитывайте, что развесовка по осям изменилась.
При вывешивании на домкрате такой автомобиль может упасть.
Работайте только на ровной нескользкой площадке, под
невывешенные колеса подкладывайте надежные упоры.
Масла, особенно
отработанные, при регулярном контакте с ними способствуют
возникновению кожных заболеваний, в т.ч. онкологических. При
попадании масла на руки вытрите их ветошью, а затем протрите
специальным препаратом для чистки рук (или подсолнечным
маслом) и вымойте теплой водой с мылом или средством для
мытья посуды. Нельзя мыть руки горячей водой, т.к. при этом
вредные вещества легко проникают через кожу. При попадании
на руки бензина, керосина или дизельного топлива вытрите их
чистой ветошью, а затем вымойте с мылом.
При работе с аккумуляторной
батареей (электролит почти всегда присутствует и на ее
поверхности) обязательно надевайте очки и защитную одежду, в
т.ч. резиновые перчатки.
Электролит при попадании на
кожу вызывает ее покраснение, жжение. Если электролит попал
на руки или в глаза, смойте его большим количеством холодной
водой (нельзя мыть с мылом!), затем руки следует вымыть
раствором питьевой соды или нашатырного спирта.
Помните, что серная кислота
даже в малых концентрациях разрушает органические волокна –
берегите одежду.
В охлаждающей жидкости
(антифризе) содержится этиленгликоль, который ядовит при
попадании в организм и (в меньшей степени) при контакте с
кожей. При отравлении антифризом нужно немедленно вызвать
рвоту, промыть желудок, а при тяжелом отравлении, приняв
солевое слабительное, обратиться к врачу. При попадании на
руки – смыть большим количеством воды с мылом. То же
относится и к тормозной жидкости. |
|
|
|
|
|
|
Лист |
|
|
|
|
|
40 |
Изм. |
Лист |
№ документа |
Подпись |
Дата |
Не открывайте пробки системы
охлаждения на горячем двигателе.
Бензин, дизельное топливо,
масла, тормозная жидкость почти не перерабатываются
естественным путем. Тормозная жидкость содержит ядовитые
гликолевые эфиры; масла – отработавшие минеральные и
органические присадки, сажу, смолы, продукты износа.
Свинцовые аккумуляторы, помимо свинца, содержат сурьму и
другие элементы, образующие высокотоксичные для живых
организмов соединения, долго сохраняющиеся в почве.
Оставляйте отработавшие материалы в пунктах утилизации.
В производственных помещениях, где производится техническое
обслуживание
автомобилей,
существует система пожарной безопасности, которая
состоит из:
-
автоматических средств тушения пожара (сплинкерная
система);
-
ручных средств (пожарные краны, шланги, брандспойты,
огнетушители, хим.порошки).
На территории
автотранспортного предприятия от всего персонала требуется
безукоризненное исполнение всех правил пожарной
безопасности: курение разрешено только в отведенных местах,
запрещено пользоваться открытым огнем, бензином для
мойки деталей. Особое
внимание необходимо обращать на хранение
легковоспламеняющихся материалов, чистоту помещений и
исправность электропроводки и электрических приборов,
а также производство сварочных, медицинских и молярных
работ.
Пожары можно тушить веществами, которые способствуют
понижению температуры
горения (вода)
или изоляции горящих предметов от доступа кислорода (песок,
огнетушительная пена). Однако нельзя тушить водой горючие
жидкости, плотность которых меньше плотности воды, т.к. эти
жидкости всплывают и продолжают гореть.
Химические
порошки применяют для тушения горящих электродвигателей,
двигателей внутреннего сгорания, ацетилена и других веществ,
которые нельзя тушить
водой. |
|
|
|
|
|
|
Лист |
|
|
|
|
|
41 |
Изм. |
Лист |
№ документа |
Подпись |
Дата |
Главным компонентов этих порошков является двууглекислая
сода, смешиваемая с
песком,
инфузорной землей, тальком. При тушении сухим порошком пламя
сбивается твердой
массой порошка и засыпается им, а образующийся при
нагревании и разложении двууглекислой соды углекислый
газ изолирует горящий предмет от доступа кислорода воздуха.
Кроме того, на разложение соды расходуется часть теплоты,
что вызывает охлаждение
поверхности горящего вещества.
Углекислый газ
применяют двумя способами: заполняют газом закрытое
помещение, где произошло возгорание, или покрывают из
специальных приборов поверхность горящего материала
углекислым газом при температуре 78° С. после заполнения
углекислым газом одной трети объема воздуха помещения
горение прекращается.
Для
экстренного тушения пожара подручными средствами во всех
помещениях и особенно
связанных с нахождением и использованием горючих веществ,
должны быть в необходимых количествах песок, пожарные
краны, хим. или углекислотные огнетушители.
|
|
|
|
|
|
|
Лист |
|
|
|
|
|
42 |
Изм. |
Лист |
№ документа |
Подпись |
Дата |
7. Список использованной
литературы
1.
Беляев С.В. Моторные масла и смазка двигателей:
Учебное пособие. Петрозаводский гос.ун-т. Петрозаводск, 1993
– 70 с.
2.
Грамолин А.В., Кузнецов А.С. Топливо. Масла, смазки,
жидкости и материалы для эксплуатации и ремонта автомобилей.
М.: Машиностроение, 1995 – 63 с.
3.
Карагодин В.И., Шестопалов С.К. Слесарь по ремонту
автомобилей: Практическое пособие -2-е изд., перераб. и доп.
М.: Высшая школа, 1990 – 239 с.
4.
Ремонтируем ВАЗ-2106, -21061. Иллюстрированное
руководства. М.: ЗАО «КЖИ «За рулем», 2004. – 216 с., ил.
(Серия «Своими силами»).
|
|
|
|
|
|
|
Лист |
|
|
|
|
|
43 |
Изм. |
Лист |
№ документа |
Подпись |
Дата |
|
|
|
|
|
|
|
|
|
|
|
|
|